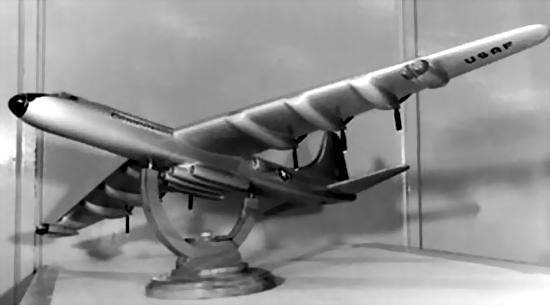
The difficulties of building a nuclear aircraft were vastly greater than building a nuclear submarine. Central among them was the need to build a reactor that could reliably provide heat at the high-temperatures needed to drive a turbojet. In a conventional turbojet engine, cold ambient air is drawn in the intake, compressed to high pressures in the compressor, and then heated to high temperature in the burner by mixing and combusting a small amount of jet fuel. The hot gas then expands through a turbine, generating the shaft power to drive the compressor, and is exhausted through the nozzle, creating thrust.
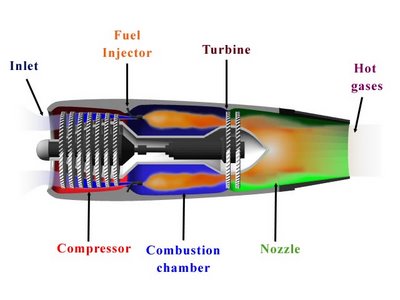
To build a nuclear-powered aircraft, the heat generated by combustion had to be replaced with heat generated by a nuclear reactor. But the typical water-cooled reactors favored for submarine proplusion could not provide heat at nearly the temperatures needed for aircraft propulsion. Beyond the high temperature requirements, the reactor needed to be extremely simple and easy to operate, since most of the crew would be occupied in flying the aircraft.
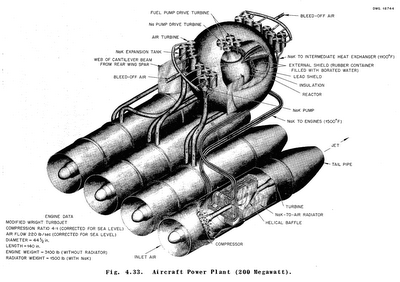
Even since the days of the Manhattan Project, some nuclear engineers had wondered if a low-melting point liquid might be a better form for nuclear fuel than a high-melting point solid. Their reasoning had mostly been centered around the ease of reprocessing a liquid-fuel form, but there were other important advantages as well. A liquid-fuel would expand when heated, creating a strong negative temperature coefficient. It could be easily drained in the event of a loss-of-coolant into a passively-cooled form. And the fuel concentration in the liquid could be altered much more readily than a solid fuel form.
Different fluid-fuels had been considered, most of them based on uranium compounds that could be dissolved in water, such as uranyl sulphate. But water-based reactors couldn't reach the temperatures needed for aircraft propulsion, even under extreme pressure. A fluid that was stable at high temperatures was needed, and stability at high temperatures implied chemical stability. Thought was given to using hydroxides as a solvent fluid, but hydroxides had limited stability at high-temperatures and were extremely corrosive to most metal structures.
In 1951, Ray Briant was a chemist working on nuclear aircraft propulsion at Oak Ridge National Laboratory. At that time, a beryllium-oxide moderated, sodium-cooled reactor with solid fuel elements was favored, but temperatures that would be attained in the reactor (1600°F) made it difficult to conceive that the fuel elements would survive long. Briant believed that such a reactor would have fuel elements that would look like "a bunch of spaghetti".
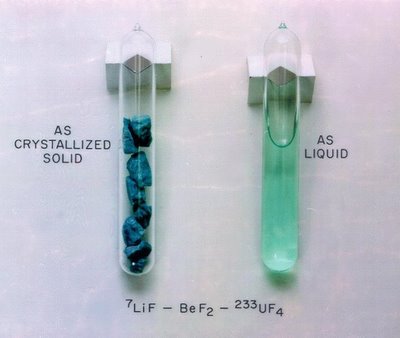
He tried to conceive of a reactor that could operate stably at such temperatures and naturally began to think about a fluid fuel form. Briant’s colleagues, Vince Calkins and Ed Bettis, proposed the fluorides of the alkali- and alkaline-earth metals as solvents, but the behavior of uranium fluoride in these salts was unknown. At first blush, however, the fluoride salts had many advantages. They were extremely chemically stable, and thus could attain very high temperature operation. But could they be used in a reactor?
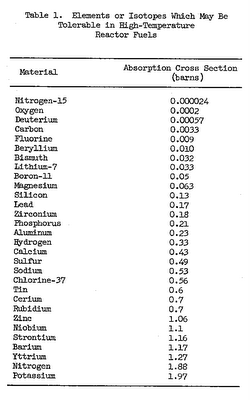
The possibility of a high-temperature, high-power density reactor was very tempting, and so an effort to prove the concept of the liquid-fluoride reactor began. A small research reactor that was being designed for the Aircraft Nuclear Program was modified to serve as a testbed for the liquid-fluoride concept. Since blocks of beryllium oxide had already been ordered for the previously-favored concept, the decision was made to use them and flow the fluoride salt through Inconel tubes in and out of the beryllium oxide block to simulate reactor performance. Thus the Aircraft Reactor Experiment was born.
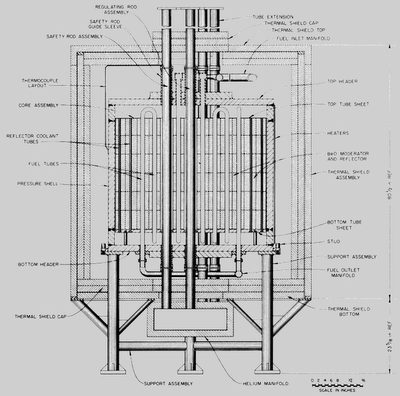
The ARE went critical for the first time on November 3, 1954 using a mixture of sodium fluoride, zirconium fluoride, and uranium tetrafluoride. It operated for a total of 100 hours at a maximum temperature of 1600°F and a maximum power of 2.5 MW (thermal). Heat generated in the fluoride salt was removed by a liquid sodium coolant loop and then dumped in an air-cooled heat exchanger. The ARE showed that not only was the UF4 chemically stable in the solvent, but also that the fission products generated by fission formed stable fluorides in the salt mixture and did not plate out on surfaces. Another surprise was that gaseous fission products were removed essentially automatically by the pumping action of the reactor, accumulating in the pump bowl above the reactor. The fluid fuel had a very strong negative temperature coefficient, and the reactor could easily be started and stopped by changing the power demand on the reactor, without control rods. Despite its success, the engineers were not anxious to run the reactor for an extended period, since the “in-and-out” tubular configuration could not drain the salt from the core in the event of an accident. After 8 days the reactor was shut down.
Flushed with success from the ARE, ORNL engineers proposed the liquid-fluoride reactor as the baseline for the Aircraft Reactor Program and it was selected. Plans were made to build a “real” liquid-fluoride reactor that would operate at 60 MWt and would be of a flight-like configuration. This reactor was to be called the Aircraft Reactor Test, but the engineers referred to it as the “Fireball”. The Fireball was a reflector-moderated design that used the NaF-ZrF4-UF4 fuel of the ARE, but was moderated by beryllium metal and cooled by liquid sodium-potassium eutectic (NaK). The NaK was planned to carry the fission heat to the turbojet engines that would provide thrust to the aircraft in flight.
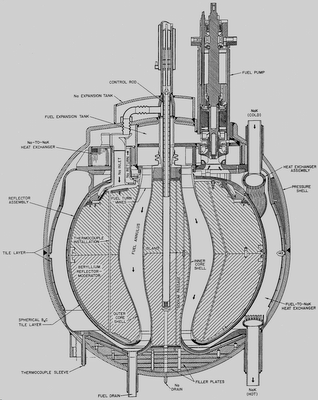
Despite the technical triumph of the liquid-fluoride reactor, the Aircraft Nuclear Program faced severe technical difficulties from the weight of radiation shielding (necessary to protect the pilot and crew) and the advent of alternative forms of nuclear weapons delivery, such as the intercontinental ballistic missile. After Kennedy took office in 1960, the ANP was quietly discontinued after the expenditure of $880 million.
ORNL interest in the liquid-fluoride reactor did not wane, however. The high-temperature performance of the reactor coupled with its neutron economy and operational stability led ORNL engineers to propose the LFR as a civilian power reactor. At first, the LFR as a converter reactor was the proposed application, but further investigation of the properties of uranium-233 led engineers to propose the LFR as a thermal breeder reactor.
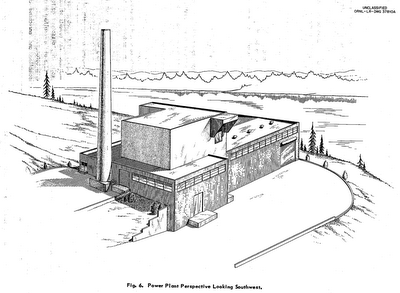
As a breeder, the LFR had some distinct advantages over other breeder concepts.
1. U-233 has the highest η (neutrons emitted per neutron absorbed) at thermal energies of any nuclide; but it was significantly less than the η expected from Pu-239 at fast energies. Thus, exceptional neutron economy was very important, and the lack of internal components in the graphite-moderated LFR led to very high neutron economy.
2. Xe-135 could be removed continuously from the LFR, significantly improving neutron economy and eliminating the issues with xenon transients that dogged reactor startup and shutdown.
3. After Th-232 absorbs a neutron, it becomes Th-233 and then decays (with a half-life of 22.3 min) to protactinium-233, which has a half-life of 27.0 days and a sizeable thermal neutron cross-section. Once formed, Pa-233 should be sequestered from the reactor and allowed to decay to U-233; otherwise it will absorb a neutron and form Pa-234 then U-234, which is not fissile. The fluid fuel nature of the LFR allows newly formed Pa-233 to be isolated from the fuel (or blanket), allowed to decay, and then reinserted into the fuel. This remarkable process is simply not possible in a solid-fueled thorium reactor—they must rely on low neutron flux to avoid protactinium destruction, which severely penalizes performance.
4. The low breeding margin for thorium-uranium means that breeders cannot afford to waste neutrons on control rods and burnable poisons. The strong negative temperature coefficient of the LFR allows stable operation at a large variety of power settings with very little absorptive-type control.
5. Thorium forms a tetrafluoride that is stable and dissolves high concentrations in the lithium-beryllium fluoride mixtures used.
The Molten-Salt Reactor Program (MSRP) was begun at ORNL under H.G. “Mac” MacPherson in 1958 and came to include many of those who had worked on the ARE. The MSRP won permission from the AEC to build a small reactor on the condition that it have less than 10 MW of thermal power.
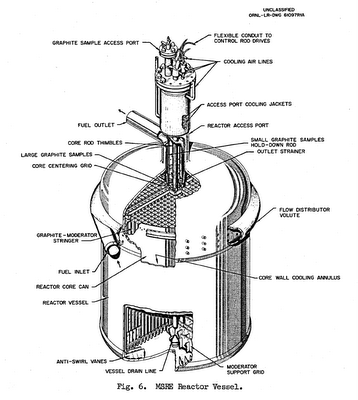
Design and construction of the Molten-Salt Reactor Experiment (MSRE) began in 1961. It was a "true" liquid-fluoride power reactor. It utilized a lithium7-beryllium fluoride solvent into which was dissolved zirconium and uranium tetrafluorides. The goal of thorium breeding was deferred since the favored design at the time was a two-region liquid-fluoride breeder. The MSRE was designed to simulate the “core” of that future reactor.
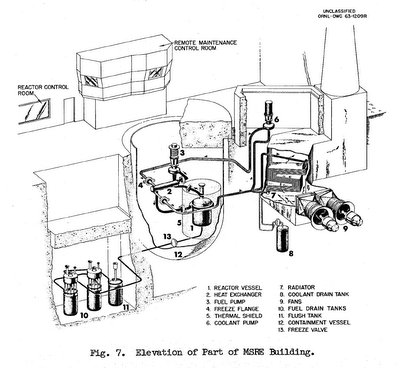
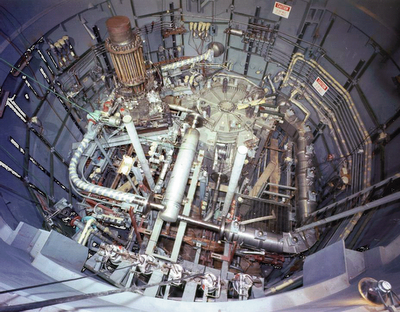
The MSRE went critical on June 1, 1965 and operated for 4.5 years until it was shut down in December 1969. The MSRE was the first (and probably only) reactor to operate on all three fissile fuels: U-233, U-235, and Pu-239. During its operation, uranium was completely removed from the salt through fluorination by bubbling gaseous fluorine through the salt. The fluorine caused the uranium tetrafluoride to convert to uranium hexafluoride, which is gaseous, and could then be removed. In 4 days, 218 kg of uranium was separated from the intensely radioactive fission products and its activity was reduced by a billionfold. The reactor was then loaded with U-233 that had been made by early runs of thorium fuel at the Indian Point reactor in New York.
When restarted, the MSRE was operating on U-233 and the Pu-239 that remained from the previous operation on 20% enriched uranium.
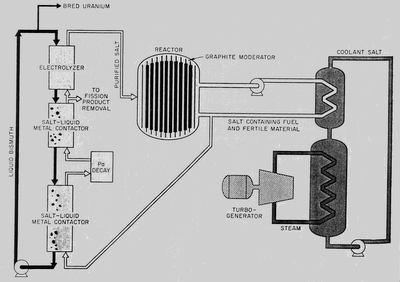
Despite its success, the AEC was heavily committed to the sodium-cooled fast breeder and the military was very interested in the high-quality, weapons-grade plutonium that would be generated by future fast breeders. The thermal-breeder operating on thorium simply could not compete on this count, and the AEC moved to cancel the MSRP in 1972. They commissioned a report (WASH-1222) that was highly critical of the liquid-fluoride reactor concept and praised the liquid-metal fast breeder. Ironically, this report omitted nearly all of the inherent safety of the liquid-fluoride reactor, its fast response to transients, its neutron economy, proliferation-resistance, and reprocessability. Instead, it focused on a few minor issues that had cropped up during MSRE operation, such as tritium generation, tellurium cracking, and graphite replacement. The program was subsequently cancelled in January 1973.
It 1974, the program was briefly restarted and solutions were pursued to tellurium-cracking and tritium isolation. These were basically solved to the satisfaction of the engineers, but a follow-on the MSRE was not approved by the AEC and the program was terminated again in 1976. The AEC’s heavy commitment to LMFBRs ended up being a great failure, with the cancellation of the Clinch River LMFBR and the subsequent end of most LMFBR research programs around the world over the last 30 years.
In retrospect, many of the reasons that the LFR was originally terminated would be selling points for the reactor today.
1. Inherent safety. The strong negative temperature coefficient of the fluid fuel, its response to transients, the stability of fission products in the salt, and the ability to drain the core into a passively-cooled configuration have led many to conclude that the liquid-fluoride reactor is probably the safest reactor ever designed. Such issues of passive safety were not of primary concern when the LFR was compared to the LMFBR in the early 1970s. Typical passively-safe nuclear reactor designs usually involve drastic performance reductions to the reactor, such the PIUS concept where the reactor is isolated in a pool of highly borated water. The LFR does not compromise performance for safety since the safety is inherent in the fuel form.
2. High performance. The LFR can operate at the high-temperatures and low pressures needed for high-efficiency electrical production from gas turbines or high-temperature thermochemical hydrogen production. Such high temperatures were almost considered a nuisance when the LFR was coupled to a steam system in the old ORNL designs.
3. Fuel cycle. The neutron economy of the LFR allows it to breed thorium to uranium and essentially run forever. Thorium is plentiful and the resources available would fuel planetary energy production for thousands of years. The DOE recently disposed of a stockpile of 3216 metric tonnes of thorium nitrate that if burned in liquid-fluoride reactors would provide all US energy (electricity and transportation) needs for five years. Fission products can be isolated from the salt and disposed in a geological repository, where their activity would drop below background levels in ~300 years. Actinides would be retained in the core and not end up in the geological repository. The generation of trans-uranic nuclides from the thorium-uranium cycle is essentially zero.
4. Operability and reliability. The LFR can be refueled continuously and easily while online, which would improve the competitiveness of utilities by eliminating refueling shutdowns. The composition of the salt is continuously re-homogenized by pumping the salt through the core. There are no “hot channels” or local burnup in a liquid-fluoride core due to this action, and not need for fuel reshuffling. Fuel can be removed easily by draining the core. The strong negative temperature coefficient allows the reactor to “follow the load” without operator intervention, and to reduce power generation extremely rapidly in response to “loss of load” accidents.
5. Response to accidents or sabotage. A properly-designed LFR can withstand accidents of tremendous magnitude such as a breach of vessel and containment, whether intentional or accidental. If the fuel salt were inadvertently exposed to the outside environment through a combined breach of containment and vessel, the salt would freeze and occlude fission products in the salt as stable fluorides. Gaseous fission products are removed from the salt in normal operation and would not comprise much of the fission product inventory. In the event of complete power loss and no backup power or cooling, the reactor would melt a plug of frozen salt in the bottom of the reactor and drain into a passively-cooled, noncritical configuration. Thus reactor operators could conceivably turn off all power and walk away from a full-power reactor and it would passively “safe” itself without incident.
No comments:
Post a Comment